إن خطة الكل أو لا شيء تعارض استخدام الجداول لفحص قبول الجودة العشوائي. إدواردز ديمينج
"لا يمكن تكييف استخدام جداول فحص عينات القبول لتقليل متوسط التكلفة الإجمالية لفحص المواد الواردة وعواقب السماح للمواد المعيبة بالدخول إلى الإنتاج."
مصدر المواد المقتبسة: [2] - دبليو. إدواردز ديمينغ، "الخروج من الأزمة" ("الخروج من الأزمة"، دبليو. إدواردز ديمينغ - م: دار نشر ألبينا، 2017. المحررون العلميون واي. روبانيك، واي. أدلر ، ف. شبير). يمكنك شراء الكتاب من الناشر ألبينا الناشر .
المقال من إعداد المدير العلمي لمركز AQT سيرجي ب. غريغورييف
حرية الوصول إلى المقالات لا تقلل بأي حال من الأحوال من قيمة المواد الموجودة فيها.
مقدمة
هل يجب أن نحاول رفض بعض أو كل العناصر المعيبة في الشحنة الواردة؟ أم يجب أن نرسل كل دفعة، متجاوزين الفحص، مباشرة إلى الإنتاج؟ الحل السليم اقتصاديًا هو استخدام خطة التحكم "الكل أو لا شيء" للمواد الخام والمواد والمكونات الواردة التي اقترحها إدواردز ديمنج.
على أية حال، لا ينبغي أن يصل أي منتج من إنتاج الشركة لا يلبي المتطلبات إلى المشتري.
يتم استخدام قاعدة التحكم في المدخلات الكل أو لا شيء لتقليل متوسط التكلفة الإجمالية للشركة لكل وحدة إنتاج. قاعدة "الكل أو لا شيء" هي قاعدة لاتخاذ قرار بشأن التحكم بنسبة 100% في دفعة واردة من المواد مع رفض المواد المعيبة أو إطلاق هذه الدفعة في الإنتاج دون سيطرة واردة، يليها استبدال وإعادة صياغة نسبة المنتجات المعيبة التي تشكلت نتيجة لمثل هذا المرور دون سيطرة واردة.
إذا قمت بإجراء فحص وارد للمواد الخام والمواد والمكونات للتحكم في العينات، فمن الأفضل معرفة ما يلي:
"إذا كانت درجة الرقابة الإحصائية على جودة المواد الواردة عالية، فإن مراقبة العينات لن توفر نظرة ثاقبة على ما تبقى من الدفعة التي تم تفتيشها، وذلك لعدم وجود دليل على الارتباط بينهما في هذه الحالة."
تأكيد عملي لمقولة إدواردز ديمنج بأن مراقبة أخذ العينات، على سبيل المثال، استخدام جداول مراقبة جودة القبول العشوائي لا يعطي فكرة عن عدد المنتجات المعيبة في الدفعة الخاضعة للرقابة، يمكن أن يكون تجربة مع الخرز الأحمر ، حيث تعطي العينات الميكانيكية العشوائية من خليط من الخرز الأحمر والأبيض في كل مرة قيمة لنسبة الخرز الأحمر التي تختلف عن النسبة الحقيقية للخرز الأحمر في الخليط المتحكم فيه، سواء الأعلى أو الأدنى. استخدمت التجربة مخطط np للتحكم في عدد الخرزات الحمراء للعينات ذات الحجم نفسه.
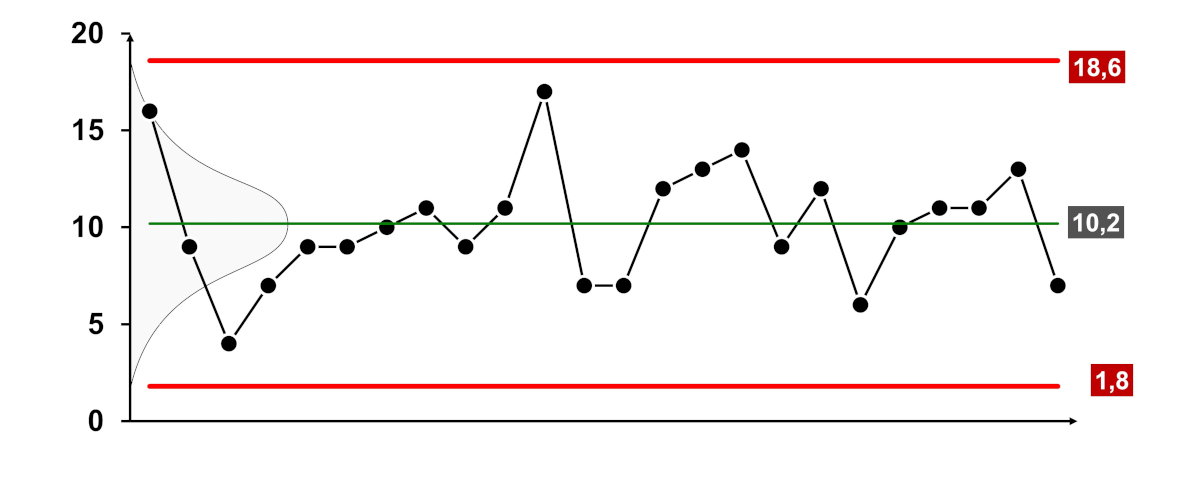
أرز. مخطط التحكم np لتجربة الخرزة الحمراء التي أجراها إدواردز ديمنج في عام 1983.
"تبين أن قواعد تقليل إجمالي متوسط التكاليف بسيطة للغاية في ظل بعض الظروف.
التسميات:
p هو متوسط نسبة المنتجات المعيبة في دفعة الأجزاء الواردة؛
ك 1 - تكلفة التفتيش الوارد لجزء واحد؛
ك 2 - تكلفة تفكيك وإصلاح وإعادة تجميع وإعادة اختبار الوحدة التي تعطلت بسبب دخول جزء معيب إلى الإنتاج.
الحالة 1:
أسوأ دفعة واردة سيكون لها متوسط معدل معيب (p) أقل من (k 1 /ك 2 ).
ص<ك 1 /ك 2
في هذه الحالة: لا يوجد تحكم في الإدخال. ويجب الاعتماد بشكل كامل على الفحص عند نقطة اختبار المكونات.
شرح، سيرجي ب. غريغورييف:
اشتقاق معادلة الشرط 1، عندما تكون التكلفة الإجمالية لتصحيح جميع الوحدات ذات الأجزاء المعيبة من الدفعة الواردة (N×p×k) 2 ) ستكون أقل من تكلفة فحص جميع الأجزاء الواردة بنسبة 100% (N×k 1 ).
(ن) - حجم الدفعة الواردة من الأجزاء وأجهزة الكمبيوتر مع حصة الأجزاء المعيبة (ع):
ن × ع × ك 2 < ن × ك 1
تقليل التعبير إلى:
ص × ك 2 <ك 1
ثم:
ص<ك 1 /ك 2
الحالة 2:
أفضل دفعة واردة ستحتوي على نسبة من العناصر المعيبة (ع) أكبر من (ك 1 /ك 2 ).
ص>ك 1 /ك 2
في هذه الحالة: التحكم في الإدخال بنسبة 100%. وتنفيذ الرقابة عند نقطة اختبار المنتجات النهائية.
شرح، سيرجي ب. غريغورييف:
اشتقاق صيغة الشرط 2، عندما تكون التكلفة الإجمالية لتصحيح جميع الوحدات ذات الأجزاء المعيبة من الدفعة الواردة (N×p×k 2 ) ستكون أكبر من تكلفة فحص جميع الأجزاء الواردة بنسبة 100% (N×k 1 ).
(ن) - حجم الدفعة الواردة من الأجزاء وأجهزة الكمبيوتر مع حصة الأجزاء المعيبة (ع):
ن × ع × ك 2 > ن × ك 1
تقليل التعبير إلى:
ص × ك 2 >ك 1
ثم:
ص>ك 1 /ك 2
(ك 1 /ك 2 ) - جودة التوازن، أو نقطة التوازن.
(ك 2 ) سيكون دائمًا أكبر (ك 1 );
وبالتالي فإن النسبة (ك 1 /ك 2 ) سوف تقع بين 0 و 1.
إذا قمت بتطبيق قاعدة الشرط 2 في موقف حيث يجب تطبيق قاعدة الشرط 1، فستكون التكلفة الإجمالية هي الحد الأقصى. والعكس صحيح أيضاً."
مثال (سيرجي ب. غريغورييف)
منح:
ع (متوسط نسبة العناصر المعيبة في دفعة الأجزاء الواردة) = 0.05؛
ك 1 (تكلفة الفحص الوارد لجزء واحد) = 100.00 ₽؛
ك 2 (تكلفة تفكيك وإصلاح وإعادة تجميع وإعادة اختبار الوحدة التي فشلت بسبب وجود جزء معيب في الإنتاج) = 1,000.00 ₽؛
مجموعة الإدخال = 1,000.00 قطعة.
الشرط 1: ع <ك 1 /ك 2 - لا يوجد تحكم في الدخول.
الشرط 2: ع>ك 1 /ك 2 - التحكم في الوارد بنسبة 100%.
العمليات الحسابية
ع = 0.05
ك 1 /ك 2 = 100.00 ₽ / 1,000.00 ₽ = 0.10
0.05 <0.10
ص<ك 1 /ك 2 - يتوافق مع الشرط 1 - لا يوجد تحكم في الإدخال.
حل
حدد خطة "لا سيطرة".
التحقق من الحل
تكلفة التحكم بنسبة 100% عند المدخل ستكون:
1,000 قطعة.×100.00 ₽=100,000.00 ₽
تكلفة تمرير المواد المعيبة ستكون:
1,000 قطعة.×0.05×1000.00 RUR=50,000.00 RUR
وبالتالي، فإن السماح بدخول جزء معيب إلى الإنتاج، في هذه الحالة، مع التفكيك والإصلاح وإعادة التجميع والاختبار اللاحق للوحدة التي فشلت بسبب دخول جزء معيب إلى الإنتاج، سيكلف بالفعل 50.000.00 أقل من 100٪ من الفحص الوارد ₽.
"وهكذا، تتمتع حالة التحكم الإحصائي بميزة واضحة. لمعرفة ما إذا كان تدفق الدفعة الواردة يفي بالشرط 1 أو الشرط 2 أو أنه في حالة تقترب من الفوضى، يحتاج المرء فقط إلى تتبع التحكم الإحصائي ومتوسط المعدل المعيب باستخدام المخططات المبنية على أساس تجارب العينات الصغيرة الجارية (كما هو الحال في أي حالة)، ويفضل أن يتم ذلك بالتعاون مع المورد وفي مقره."
شروط أخرى لوحظت في الممارسة العملية (إدواردز ديمنج)
موقع متوسط للتوزيع مع انحراف معتدل عن إمكانية التحكم الإحصائي.
سنقوم الآن بتحليل نوعين من المواقف الوسيطة لتوزيع نسبة العناصر المعيبة في الدفعات الواردة. ربما، باستخدام مخططات التحكم الخاصة بنا، أو مخططات الموردين، أو المخططات التي يتم الاحتفاظ بها بشكل مشترك، يمكننا التنبؤ بأن جزءًا صغيرًا فقط من التوزيع سوف يقع على يمين نقطة التوازن. في هذه الحالة يمكننا اعتماد قاعدة "عدم السيطرة". ستسمح لنا هذه القاعدة بالاقتراب من الحد الأدنى لمتوسط إجمالي التكاليف، بشرط أن يكون جزء التوزيع الذي يقع على يمين نقطة التوازن صغيرًا.
الوضع المعاكس: جزء صغير فقط من توزيع حصة المنتجات المعيبة في الدفعات الواردة يقع على يسار نقطة التوازن. بمعرفة ذلك، يمكنك قبول قاعدة التحكم بنسبة 100% في الدفعات الواردة بأمان.
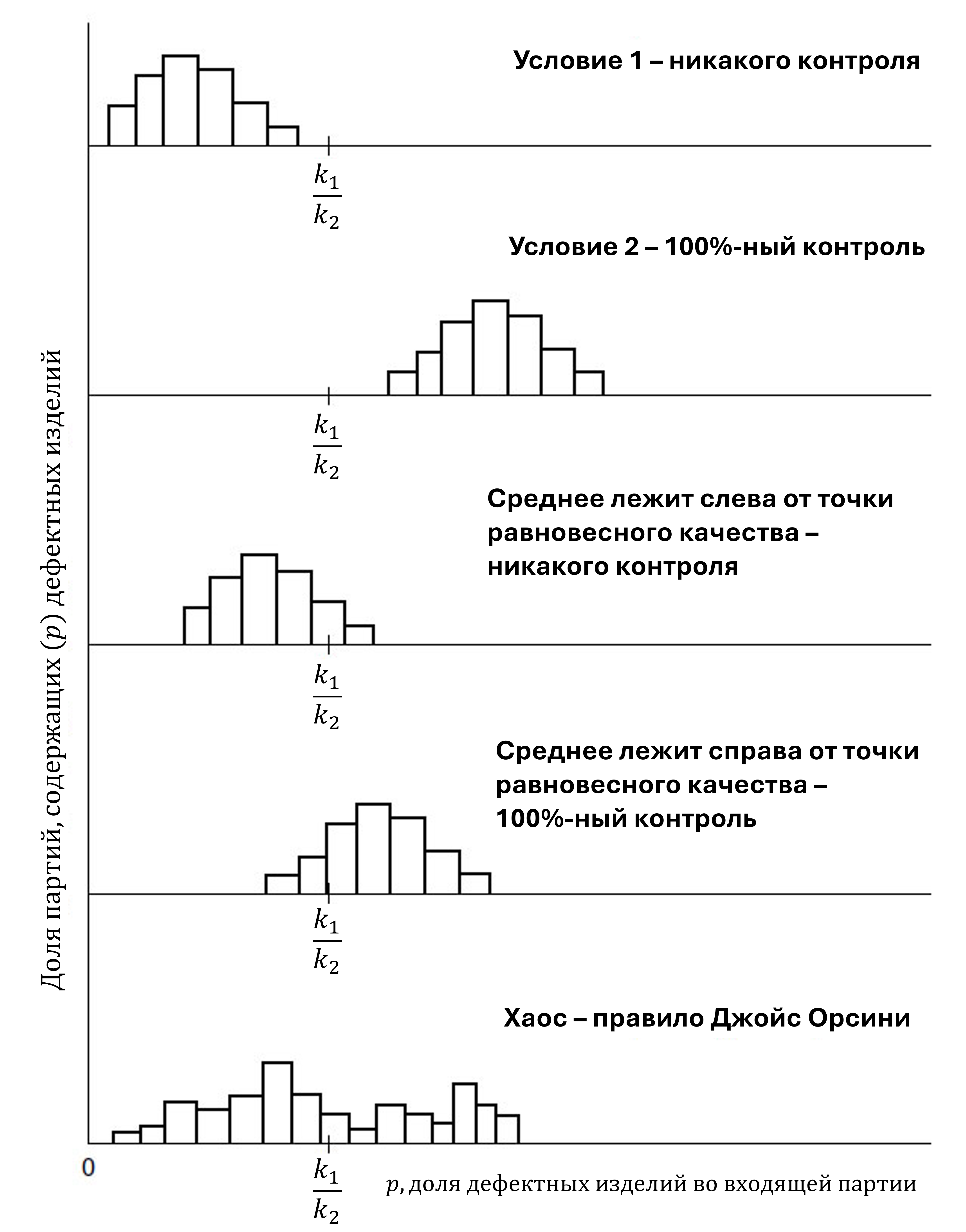
أرز. 1. المواقف المحتملة عند استلام المنتجات الواردة على دفعات.
النقطة B هي نقطة جودة التوازن، حيث p = k
1
/ك
2
. مصدر:
[2]
إدواردز ديمنج، الخروج من الأزمة
الاتجاه في حصة المنتجات المعيبة في الدفعات الواردة
لنفترض أن هناك اتجاهًا قد تشكل نحو زيادة نسبة المنتجات المعيبة. اليوم نحن في الحالة 1 ولا سيطرة لنا عليها، ولكن (ع) تعتمد على الزمن وتتزايد ربما بمعدل ثابت وربما بشكل غير منتظم. خلال يومين سوف ندخل منطقة الحالة 2: لقد تم تحذيرنا. ستكشف مخططات التحكم الخاصة بالمورد أو مخططاتنا عن الاتجاه في حالة وجوده. يمكن حل هذه المشكلة بسهولة.
المشاكل الناجمة عن التبديل بين الموردين المختلفين
بسبب التغيرات في مصادر المواد عند مدخلات النظام، تنشأ المشاكل دائما. دعونا نقتصر على النظر في مصدرين. إذا كان كلا المصدرين خاضعين لرقابة إحصائية جيدة أو متوسطة ويمكن فصلهما عن بعضهما البعض، فمن حيث المبدأ، فإن كل مصدر يفي بالشرط 1 أو الشرط 2، اعتمادًا على ما إذا كان متوسط ذلك المصدر يقع إلى يسار أو إلى يمين نقطة التوازن. هذه الفكرة بسيطة بالكلمات، ولكن قد يكون من الصعب تنفيذها في بعض النباتات.
إذا تم خلط المواد من مصدرين بشكل متجانس بنسبة ثابتة، وإذا أظهر كلا المصدرين تحكمًا إحصائيًا كافيًا، فيمكن اعتبار الدُفعات المختلطة بمثابة خليط ذي الحدين، ويمكن تحقيق الحد الأدنى من متوسط تكلفة التحكم باستخدام الكل أو لا شيء قاعدة.
المواد من مصدرين تجلب مشاكل إضافية للإنتاج. إن الخليط المتجانس من المواد من مصدرين هو السيناريو الأسوأ بالنسبة لمدير التصنيع.
الخطوة الأولى هي تقليل عدد الموردين إلى مورد واحد. إذا تم توفير منتج ذو جودة متغيرة من مصدر واحد، فيجب على المورد وعميله العمل معًا لتحسينه، بهدف تلبية الشرط 1 وتحقيق صفر عيوب في النهاية.
حالة من الفوضى
إن تحديد ما يجب فعله في موقف يتقلب فيه موضع التوزيع قليلاً بالقرب أو أبعد من نقطة التوازن أمر سهل نسبيًا.
بالقرب من نقطة التوازن، لا يهم حقًا ما إذا كان لدينا سيطرة بنسبة 100٪ أو لا سيطرة على الإطلاق. سأختار التحكم بنسبة 100% لجمع المعلومات في أسرع وقت ممكن. إذا لم نتمكن من التأكيد على أن جودة المواد الواردة تقع في الغالب على يمين أو يسار نقطة التوازن، ولكنها على العكس من ذلك، تتقلب على نطاق واسع، وتمر عبر نقطة جودة التوازن، فنحن في حالة من الفوضى.
1. قد ينشأ هذا الوضع غير المقبول عندما يتم توفير المواد ذات التباين العالي والجودة غير المتوقعة من مصدر واحد.
2. قد ينجم مثل هذا الاختلاف حول نقطة جودة التوازن عن الحصول على مادة من مصدرين أو أكثر ذات جودة متفاوتة على نطاق واسع. في هذه الحالة، يتم التبديل من مصدر إلى آخر بشكل لا يمكن السيطرة عليه، دون تسلسل مدروس. يجب أن نخرج من هذه الحالة في أسرع وقت ممكن وننتقل إلى الحالة 1. لكن الدفعات تستمر في القدوم، وعلينا أن نفعل شيئًا معها. كيف يجب أن نتعامل معهم؟
إذا جاءت كل دفعة مع ملصق يخبرنا بنسبة العناصر المعيبة فيها، فلن تكون هناك مشكلة. وسوف نحقق الحد الأدنى من متوسط التكلفة الإجمالية عن طريق وضع كل دفعة، واحدة تلو الأخرى، على يمين أو يسار نقطة التوازن وتطبيق قاعدة كل شيء أو لا شيء من دفعة إلى أخرى.
ولكن لم يتم وضع علامة على دفعات. ومع ذلك، في حالة الفوضى هناك بعض الارتباط بين جودة المنتجات في العينة وبقية الدفعة. لذلك، في حالة من الفوضى، يمكنك اختبار العينات، وباستخدام بعض القواعد، تقرر ما إذا كنت تريد إرسال الجزء المتبقي إلى الإنتاج بالكامل أو رفضه.
إن أخذ العينات، بغض النظر عن مدى جودة استخدامه، سيؤدي إلى وصول بعض الدفعات إلى الجانب الخطأ من نقطة التوازن، مع ما يترتب على ذلك من تعظيم إجمالي التكاليف للدفعة التي تم تحديدها بشكل خاطئ.
في حالة الفوضى، قد يميل المرء نحو السيطرة بنسبة 100٪. هذا القرار منطقي بعض الشيء.
لا تترك أبدا دون معلومات
لا تعني قاعدة عدم التحكم في الدخول القيادة في الظلام مع إطفاء المصابيح الأمامية. يجب مراجعة جميع المواد الواردة (ربما تخطي بعض الدفعات) للحصول على المعلومات ومقارنة التسليم الفعلي مع مذكرات الشحن الخاصة بالمورد، وفحص اختبارات المورد ومخططات التحكم المصاحبة. إذا كان هناك موردين اثنين، فاحتفظ بسجلات لكل منهما على حدة.
النصيحة التالية هي الذهاب إلى مورد واحد لكل منتج بناءً على علاقة طويلة الأمد والعمل معهم لتحسين الجودة الواردة.
اختبار المدمرة
تعتمد النظرية السابقة على الاختبار غير المدمر للنموذج الأولي. بعض الاختبارات مدمرة؛ يقومون بتدمير العينة الخاضعة للرقابة. ومن الأمثلة على ذلك عمر المصباح الكهربائي، أو عدد السعرات الحرارية الناتجة عن حرق قدم مكعب من الغاز، أو زمن تشغيل المصهر، أو اختبار محتوى الصوف في قطعة من القماش. لن يكون من المنطقي رفض الدفعة بأكملها، لأنه لن يكون هناك شيء يمكن نقله إلى الإنتاج.
من الواضح، بالنسبة للاختبارات المدمرة، أن الحل الوحيد هو تحقيق حالة من التحكم الإحصائي في إنتاج الأجزاء من أجل تصنيعها بشكل صحيح على الفور. هذا الحل هو الأفضل لكل من الاختبارات المدمرة وغير المدمرة.
إمكانية التجميع المعيب للعديد من الأجزاء
تحدثنا في الأقسام السابقة عن المنتجات البسيطة المكونة من جزء واحد. قد تتطلب بعض الأجزاء فحصًا بنسبة 100% لتقليل التكلفة الإجمالية. وبمجرد اختبارها، فإنها لن تتسبب في فشل عملية التجميع. لن يتم اختبار الأجزاء المتبقية، والجزء المعيب، إذا دخل الإنتاج، سوف يسبب الفشل. لنفترض أن لدينا جزأين لم يتم اختبارهما.
جزأين لم يتم اختبارهما لهما أسهم معيبة 1 و ص 1 . إذن فإن احتمال فشل التجميع سيكون مساوياً لـ:
العلاقات العامة (سوف يرفض) = 1 – العلاقات العامة (لن يرفض) = 1 – (1 – ص 1 )(1 – ص 2 ) = ص 1 +ص 2 -ص 1 ص 2
إذا كانت كلا القيمتين p 1 و ص 2 - صغير، فإن هذا الاحتمال سيكون قريبًا من القيمة:
العلاقات العامة (سوف يرفض) = ص 1 +ص 2
إحدى الطرق البسيطة لكتابة احتمالية الفشل لأي عدد من الأجزاء هي استخدام مخططات فين (الموصوفة في أي كتاب عن نظرية الاحتمالات).
بشرط أن يكون كل ص أنا صغير. التعميم على أجزاء م يعطي:
العلاقات العامة (سوف يرفض) = ص 1 +ص 2 + … + ص م
وبالتالي فإن احتمال الفشل يزداد مع زيادة عدد الأجزاء. قد يحتوي الراديو على 300 جزء، على الرغم من أن هذا العدد يعتمد على كيفية عدها. يمكن أن تحتوي السيارة على 10000 قطعة، مرة أخرى اعتمادًا على كيفية العد. هل الراديو في السيارة جزء واحد أم 300؟ هل مضخة الوقود جزء 1 أم 7؟ بغض النظر عن رأيك، فإن عدد الأجزاء في مجموعة واحدة يمكن أن يكون هائلاً.
`ولكن هناك مشكلة أخرى: ك 2 (تكلفة تصحيح التجميع المعيب) تزداد مع زيادة عدد الأجزاء. عندما يفشل التجميع، أي جزء هو المخطئ؟ من السهل جدًا التشخيص الخاطئ. علاوة على ذلك، من جزأين، قد يكون كلاهما معيبًا.
بالنسبة للمنتجات التي تتكون من عدة أجزاء:
1. يمكننا السماح لعدد قليل فقط من الأجزاء بالوفاء بالشرط 2 (التحكم بنسبة 100%)؛ وإلا فإن تكلفة السيطرة ستكون باهظة.
2. بالنسبة للأجزاء الأخرى، فإن الجودة القريبة من الصفر هي المقبولة فقط.
تجميعات من مكونات معقدة
التوفير المحتمل عند إنشاء أنظمة فرعية مساعدة. في النظرية السابقة، التكلفة ك 2 يزداد عادةً (ربما زيادة بمقدار 10 أضعاف) مع كل خطوة من خطوات العملية ويمكن أن يصل إلى قيم عالية جدًا أثناء التجميع النهائي. في بعض الأحيان يمكن تجنب التكاليف المرتفعة غير الضرورية عن طريق إنشاء أنظمة فرعية تتحرك على طول التدفق المجمع وتشكل المنتج النهائي. تشكل بعض الأنظمة الفرعية، بعد أن مرت عبر التحكم وتتطلب استبدالات وتعديلات طفيفة، نقطة انطلاق جديدة. التكلفة ك 2 ستكون الآن تكلفة مراقبة وضبط النظام الفرعي. يمكن أن تظهر النظرية، إلى جانب سجلات الخبرة المفيدة، أن بعض الأنظمة الفرعية لا تحتاج إلى اختبار على الإطلاق، في حين يجب أن تخضع أنظمة أخرى للتحكم بنسبة 100٪ لتجنب زيادات التكلفة مع تقدم العملية. تتيح لك النظرية المقدمة في هذا الفصل اتخاذ القرار الصحيح.
هدفنا في الأقسام السابقة هو إظهار أن هناك طرقًا لتقليل التكاليف وتعظيم الأرباح إذا اتبعت النظرية الصحيحة.
وفي الوقت نفسه، نبذل قصارى جهدنا لإزالة المنتجات المعيبة تمامًا من العملية. نقوم بذلك بشكل منهجي من خلال مقارنة نتائج الاختبار الخاصة بنا مع نتائج المورد وتطبيق الأساليب الإحصائية المناسبة مثل مخططات X وR (مخططات التحكم Shewhart).
إن التعاون المثمر مع موردي الأجزاء، وخاصة الأجزاء الهامة منها، والاختبار والتعديل الناجح للأنظمة الفرعية، يقلل جميع المشكلات الرئيسية أثناء الفحص النهائي للأنظمة إلى الأحداث النادرة.
المواد الواردة هي منتج ثانوي للمورد
عندما تكون المادة المهمة للعميل بالنسبة للمورد منتجًا ثانويًا، تمثل أقل من 1% من أعماله. لا يمكن أن نتوقع من المورد أن يتحمل تكلفة ومخاطر تركيب المعدات لتحسين المنتج.
التوصية المحتملة هي اعتبار هذه المادة بمثابة خام حديد أو مدخلات أخرى شديدة التغير وغير منقاة. قم بتثبيت نظام تنظيف المواد الخاص بك أو استخدم خدمات شركة خارجية. هذه الخطة فعالة في بعض الحالات.
- صعوبات في اكتشاف العيوب النادرة
من الصعب اكتشاف العيوب النادرة. ومع انخفاض نسبة المنتجات المعيبة، يصبح من الصعب بشكل متزايد تحديد مدى صغر العدد. لا يمكن اكتشاف جميع العيوب باستخدام الفحص، خاصة عندما تكون نادرة، وهذا ينطبق على الفحص البصري والآلي. لا يوجد سبب للثقة في الشركة المصنعة التي تدعي أن لديها عيبًا واحدًا فقط في 10000 منتج أكثر من الشركة المصنعة التي تدعي وجود عيب واحد في 5000 منتج. وفي كلتا الحالتين، يصعب تقدير هذه النسبة.
وبالتالي، إذا كانت (p) تساوي 1/5000 وإذا كانت العملية في حالة مراقبة إحصائيًا، فيجب فحص 80000 جزء للعثور على 16 جزءًا معيبًا.
سيرجي ب. غريغورييف:
5000×16=80000
ستعطي هذه البيانات تقديرًا لمتوسط المعدل المعيب p = 1/5000 لعملية إنتاج ذات خطأ قياسي قدره σ = √16 = 4. هذا التقدير للمعدل المعيب غير دقيق، على الرغم من صعوبة مراقبة الكثير من 80.000 قطعة. السؤال الذي يطرح نفسه: هل ظلت العملية مستقرة طوال فترة إنتاج 80 ألف قطعة؟ وإذا لم يكن كذلك، فما معنى الرقم 16 منتجاً معيباً؟ سؤال صعب.
سيرجي ب. غريغورييف:
في هذه الحالة، إذا كانت عملية المورد في حالة مراقبة إحصائيًا، فمن المفترض أن تعمل حول متوسط القيمة c = 16 عيبًا للدفعات على شكل مجموعات فرعية مكونة من 80.000 جزء في الحجم مع القيم العليا (VKG) ، UCL) وحدود التحكم الأدنى (NKG، LCL) مخططات C: UCL، LCL = c ±3σ أو UCL، LCL = c ±3√c، مما يؤدي إلى انتشار القيم حول المتوسط (c=16) ضمن ±12.
يمكن العثور على الصيغ في GOST R ISO 7870-1-2011 (ISO 7870-1:2007)، GOST R ISO 7870-2-2015 (ISO 7870-2:2013) - الطرق الإحصائية. مخططات التحكم شيوهارت [أحد عشر] .
لحساب (σ)، يستخدم ديمنج مخطط C لعدد العيوب لكل منطقة تعريف ثابتة تساوي 80000 جزء.
لماذا 16؟ تتيح القيمة المتوسطة (16) حسابًا سهلاً للقيمة (σ) للمخطط C وتوفر حدود التحكم الدنيا والعليا.
وبالتالي، لكي يطالب المورد بمعدل الخلل هذا (1/5000) يتطلب فهمًا لاستقرار عملية الإنتاج الخاصة به، وهو ما لا يمكن تأكيده إلا باستخدام مخططات التحكم في Shewhart، ويجب إنشاء مخطط التحكم، على سبيل المثال، بمعدل ثماني نقاط كحد أدنى، حيث كل نقطة هي عدد العيوب لكل دفعة مكونة من 80.000 قطعة مع قيم عددية محتملة من 4 إلى 28 عيب موزعة على بحكم التجربة حول المتوسط: 16 عيبًا لكل دفعة مكونة من 80.000 قطعة.
لماذا كان من المستحيل تنفيذ هذه العمليات الحسابية البسيطة بمتوسط قيمة العيوب ج = 1 لمجال تعريف ثابت مكون من 5000 جزء؟ نعم، لأنه لن تتمكن من الحصول على نقاط من الأعداد الصحيحة لعدد العيوب في مخطط التحكم أقل من متوسط القيمة c=1، باستثناء الصفر. على الرغم من أنه من السهل رياضيا الحصول على رقم عشري في العمليات الحسابية، على سبيل المثال = 0.3، فكيف تتخيل إمكانية الحصول في الظروف الحقيقية على عدد العيوب 0.3 في دفعة مختبرة (مجموعة فرعية)؟
هناك أمثلة عندما لا يكون هناك فشل واحد في ملايين الأجزاء، أو أن عددها صغير جدًا أو أنها مفقودة في 10 مليارات. لن تساعد أي مراقبة على المنتجات النهائية في الحصول على المعلومات المطلوبة عندما تكون نسبة المنتجات المعيبة صغيرة جدًا. الطريقة الوحيدة الممكنة لمعرفة ما يحدث في مثل هذه المتطلبات القصوى هي استخدام مخططات التحكم مع القياسات الفعلية للأجزاء أثناء العملية. مائة ملاحظة، مثل 4 عناصر متتالية 25 مرة في اليوم، ستؤدي إلى 25 نقطة عينة لمخطط X وR لمتوسطات ونطاقات المجموعة الفرعية. ستوضح مخططات التحكم الخاصة بشيفارت ما إذا كانت العملية تسير دون تغيير، أو ما إذا كان الفشل قد حدث في مكان ما ويجب إيقاف إنتاج عدد من المنتجات حتى يتم اكتشاف السبب. بمجرد العثور على السبب، يمكنك أن تقرر رفض مجموعة المنتجات بأكملها لفترة معينة أو تخطي بعض المنتجات. أصبحت القدرات المتزايدة باستمرار لمخططات التحكم XbarR للمجموعات الفرعية المتوسطة والمدى أكثر وضوحًا.
سيرجي ب. غريغورييف: دونالد ويلر في المقال مخططات التحكم للبيانات البديلة (الأعداد) p-chart، np-chart، C-chart وu-chart أو مخطط XmR واحد للقيم الفردية؟ يعزز هذه التوصية من قبل إدواردز ديمنج:
"نظرًا لأنه نادرًا ما يكون من المنطقي استخدام كميات منفصلة (الأعداد) عندما يمكن الحصول على نتائج القياس، فإن استخدام السمات يقتصر عمومًا على المواقف التي يمكن فيها حساب "الأخطاء المربكة". ومع ذلك، فإن تعريف "الأخطاء المربكة" عادة ما يشكل صعوبة كبيرة. الصعوبة الرئيسية في تعريف "الخطأ المربك" هي مشكلة التعريفات الإجرائية ".
استخدام التحفظات
في بعض الأحيان يكون من الممكن والمعقول عند تصميم المعدات المعقدة وضع جزأين أو أكثر بالتوازي، بحيث إذا فشل أحدهما، فإن الآخر سيتولى وظائفه تلقائيًا. جزأين متوازيين، كل منهما متوسط معدل الخلل ص أنا ، تعادل واحدًا بمتوسط معدل معيب يساوي p أنا ². إذا، على سبيل المثال، ص أنا =1/1000، ثم ص أنا ²=1/1000000.
وبطبيعة الحال، فإن قيود الوزن والحجم قد تمنع استخدام التكرار.
هناك مخاوف أخرى: هل سيعمل الجزء الاحتياطي عند الحاجة؟ ربما يكون الحل الأفضل هو الموثوقية العالية في جزء واحد.
خاتمة
لن يتم التسامح مع المواد المعيبة والتصنيع في عملية التصنيع. تعلمنا النظرية الموضحة أعلاه مدى أهمية عدم التسامح مع المواد المعيبة في أي مرحلة من مراحل الإنتاج. منتج عملية واحدة هو مادة الإدخال للعملية التالية. المادة المعيبة، بمجرد إنتاجها، تظل معيبة حتى يتم اكتشاف الخلل، ولحسن الحظ، في وقت لاحق من الاختبار، ومع ذلك، فإن التصحيح والاستبدال لن يكون رخيصًا.
تتمتع حالة القدرة على التحكم الإحصائي بميزة واضحة. لمعرفة ما إذا كان تدفق الدفعة الواردة يفي بالشرط 1 أو الشرط 2 أو أنه في حالة تقترب من الفوضى، يحتاج المرء فقط إلى مراقبة التحكم الإحصائي ومتوسط النسبة المئوية للعناصر المعيبة باستخدام مخططات التحكم في Shewhart التي تم إنشاؤها من الاختبارات المستمرة لعينات صغيرة (كما هو الحال في أي الحالة)، ويفضل أن يتم ذلك بالتعاون مع المورد وعلى أراضيه.
الاستثناءات
العديد من المواد المدخلة لا تتبع النظرية الموضحة أعلاه. على سبيل المثال، خزان الميثانول بعد التحريك بخرطوم الهواء. عينة الميثانول المأخوذة من أي جزء من الخزان تقريبًا ستكون هي نفسها تقريبًا. ومع ذلك، تقوم شركات الكيماويات بأخذ عينات من الميثانول على عدة مستويات. ربما يكون المثال الأقرب هو أخذ عينة من الجن أو الويسكي. نحن نتفق على أنه لا يهم من أين نأخذ الحصة: من الأعلى، أو من منتصف الزجاجة، أو من الأسفل.
شرح سيرجي ب. غريغورييف: تشير الفقرة أعلاه إلى حالات استثنائية عندما يمكن أن تعزى نتيجة مراقبة العينة إلى الدفعة بأكملها.
يؤدي تسخين الفرن العالي إلى حدوث مشكلات، وهو مثال آخر لا تنطبق عليه النظرية الواردة في هذا الفصل. التدفئة ليست موحدة. بعض الشركات تأخذ عينات صغيرة من كل تعبئة. توفر هذه العينات، إذا تم تحليلها، بيانات لمخطط العملية الذي يمكن أن يُظهر اختلافات في الجودة من أول قالب إلى آخر قالب، مما يوفر أدلة على التحسينات.
شرح سيرجي ب. غريغورييف: تتناول الفقرة أعلاه حالات استثنائية عندما تكون العملية، بحكم التعريف، غير متجانسة في مراحل مختلفة من العملية مع إمكانية أخذ عينة واحدة من كل مرحلة؛ في مثل هذه الحالات، لتحليل الاختلاف بين الدفعات المختلفة (المسبوكات)، من الضروري استخدام عنصر التحكم XmR -خريطة القيم الفردية.
انظر الحل مفتوح المصدر: مشكلات استخدام جداول التحكم في جودة القبول العشوائي .